FuSy - Functional Safety of Permanent Magnet Synchronous Machines in Electric Vehicles
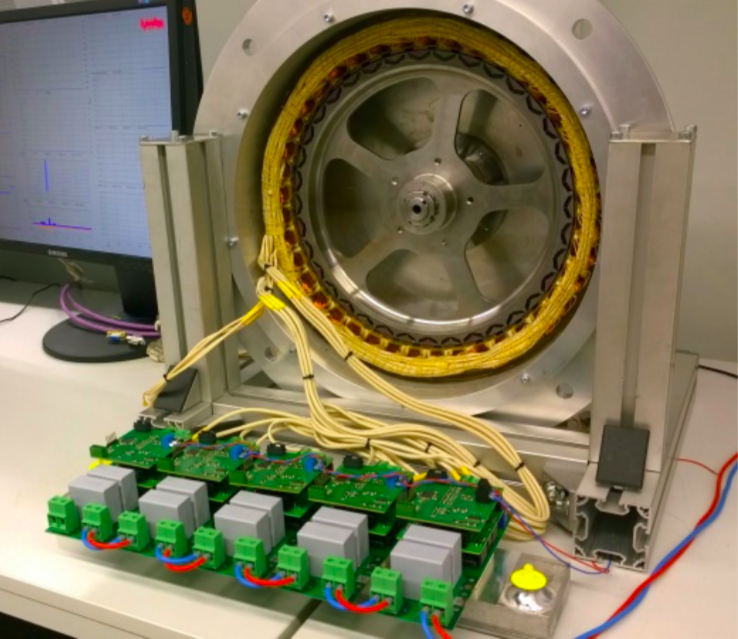
Led by: | Prof. Dr.-Ing. Axel Mertens |
Year: | 2015 |
Funding: | Bundesministerium für Wirtschaft und Energie (BMWi) |
Duration: | 3 Jahre |
Is Finished: | yes |
Fig. 1: Test bench demonstrator (source: Fraunhofer IFAM)
In drive systems using permanent magnet synchronous machines, machine or converter errors might cause critical states in the drive system. For example in the field weakening range, overvoltages might occur at the motor terminals. Other effects might be high braking or oscillating torques, leading to critical driving situations. The aim of the joint project FuSy was to avoid undesirable braking and driving torques and to increase the functional safety of permanent magnet synchronous machines used in electric vehicles. In cooperation with Fraunhofer IFAM, a novel drive monitoring and error correction concept was developed and tested in combination with alternative fault- tolerant drive topologies.
To improve error detection, new methods for detecting converter errors in the vicinity of the semiconductors were developed and successfully tested on a demonstrator at IAL. In addition, an error detection system for sensor errors in the rotor position sensor and in the current sensors were developed based on observer structures and implemented into the drive control. In case of an error, the estimates from the observers can additionally be used as redundant sensors. The error detection and correction methods were implemented into the motor control systems at IFAM.
For an optimum error correction and to avoid critical driving situations, fault-tolerant drive topologies were also designed and investigated. Besides the topology already realized in the wheel hub drive of Frecc0 using several electrically independent three- phase systems, several multi-phase topologies with single phases without star point were also set up in the laboratory. Apart from fault tolerance, such topologies, when designed appropriately, may provide for higher power densities and less torque ripple, thus compen- sating for the more complicated control method.
The test bench demonstrator (Fig. 1) is a direct drive with five independent single phases, which is fed by an inverter with five full bridges. The error detection and correction was tested on the drive system successfully. Moreover, the motor predictions could be verified by measurements. In a final step, the error detection systems were implemented in the IFAM test vehicle Frecc0. The correct operation could be verified by test drives on a test track (Fig. 2). Thanks to the excellent cooperation with IFAM in the project FuSy, a novel concept for an increased functional safety of drive systems could be developed and tested.
Fig. 2: Vehicle behaviour in case of an offset error (left) and after error correction (right) (source: LUH, IAL)
Contact Leibniz University Hannover
Prof. Dr.-Ing. Axel Mertens | |
Faculty of Electrical Engineering and Computer Science, Institute for Drive Systems and Power Electronics | |
mertens@ial.uni-hannover.de |
Consortium
Partners of Leibniz University Hannover
Further partners